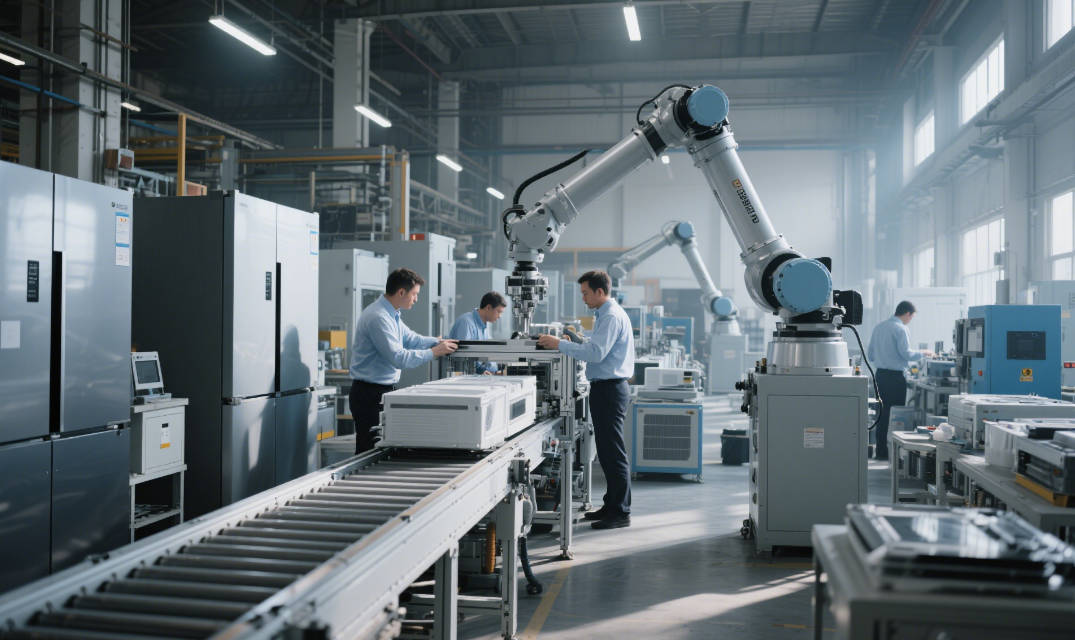
Iceboxes, a staple in commercial and residential settings, are a testament to the ingenuity of modern refrigeration technology. The development cycle of an icebox in a factory is a complex process that encompasses various stages, from ideation to the final product. This article aims to shed light on the timeline and steps involved in the factory development of an icebox.
The Conceptualization Phase
The journey of an icebox begins with its conceptualization. This phase involves brainstorming and sketching out the design, taking into account market needs, user preferences, and technological advancements. Engineers and designers work together to create a blueprint that not only meets the functional requirements but also aligns with aesthetic standards. This phase can take anywhere from a few weeks to several months, depending on the complexity of the design and the feedback loop with potential customers.
Prototyping and Testing
Once the design is finalized, the next step is prototyping. A prototype is a preliminary model of the icebox that allows for testing of various components and the overall functionality. This phase is crucial as it helps identify any design flaws or performance issues that need to be addressed before moving to mass production. The prototyping stage can take several weeks to a few months, with extensive testing and iterations to refine the product.
Tooling and Manufacturing Setup
After successful prototyping, the factory must set up the tooling and manufacturing processes. This involves creating molds, jigs, and fixtures necessary for the production of the icebox components. The setup phase can be time-consuming, often taking a few months, as it requires precision and careful planning to ensure the production line's efficiency and the quality of the final product.
Production and Assembly
With the manufacturing setup in place, the production phase commences. This is where the actual manufacturing of the icebox components takes place, followed by assembly. Depending on the complexity of the icebox and the production capacity of the factory, this phase can range from a few weeks to several months. Quality control checks are integral during this stage to ensure that each unit meets the required standards.
Quality Assurance and Final Testing
Before the icebox can be released to the market, it undergoes a rigorous quality assurance process. This includes final testing to ensure that the product performs as intended under various conditions. Any issues identified during this stage can lead to a recall of the batch forrectification, which can add additional time to the overall development cycle.
Packaging and Distribution
The final stage in the development cycle is packaging and distribution. Once the iceboxes pass all quality checks, they are packaged for shipping to distributors and retailers. This stage can take a few days to a couple of weeks, depending on the scale of production and distribution logistics.
In conclusion, the development cycle of an icebox in a factory is a multifaceted process that can span from several months to over a year. Each stage is critical and contributes to the final product's quality and market success. Understanding this timeline helps in planning and managing the production efficiently, ensuring that the icebox meets the expectations of both the manufacturer and the end-user.
This batch of products seems to be of good quality.