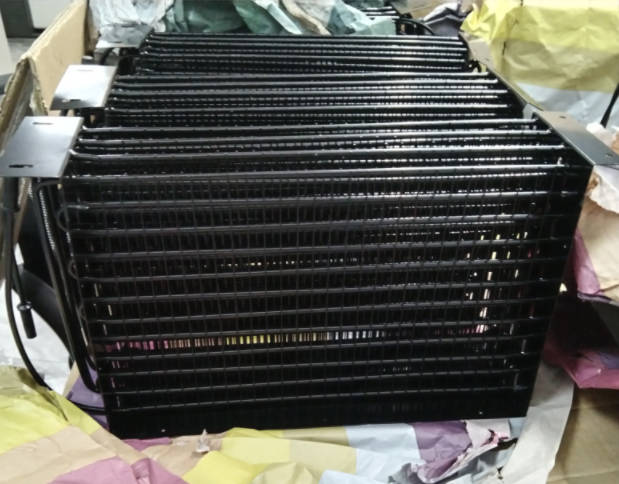
Among the numerous components of a freezer, the evaporator is one of the core components. Its main responsibility is to absorb the heat inside the freezer through the evaporation of the refrigerant, thus creating and maintaining a low - temperature environment to ensure that food is properly preserved. Under normal usage conditions, the freezer evaporator is not prone to damage, and there are several reasons behind this.
From the perspective of structural design, the structure of the freezer evaporator is relatively simple and stable. There are various common forms of evaporators. For example, the aluminum plate blown - up evaporator often used in direct - cooling freezers is formed by molding two aluminum plates and blowing them up in between. This structure gives the evaporator good integrity, reducing problems such as component loosening and wear caused by a complex structure. For the fin - tube evaporator in air - cooling freezers, by closely combining the fins with the coils, the heat - exchange area is increased. At the same time, the layout and fixing methods of the coils are carefully designed to withstand the pressure changes generated by the refrigerant flowing in the tubes and the thermal stress brought about by the alternation of heat and cold, maintaining structural stability during long - term operation.
The selection of materials plays a crucial role in the durability of the evaporator. Nowadays, most freezer evaporators are made of aluminum or aluminum - alloy materials. Aluminum has the characteristics of being soft in texture and having good heat transfer performance, which can efficiently transfer cold energy to meet the refrigeration needs of the freezer. Moreover, the chemical properties of aluminum are relatively stable, and it has good corrosion - resistance in the general usage environment of the freezer. In contrast, some other metals may be more easily affected by factors such as the humidity inside the freezer and the refrigerant, leading to rust and corrosion, thus shortening the service life. For example, iron - made materials are prone to rust in a humid environment. Once rust occurs, it not only affects the heat - transfer efficiency of the evaporator but may also cause the pipeline to perforate, resulting in refrigerant leakage and ultimately damaging the evaporator. However, aluminum - made evaporators can effectively avoid these problems and greatly improve their own durability.
Analyzing from the working environment, although the temperature inside the freezer is low and the humidity is high, the damage to the evaporator in this environment is relatively limited. On the one hand, when the evaporator is designed, the influence of the low - temperature environment is taken into account, and the selected materials and manufacturing processes can adapt to this low - temperature working condition without problems such as brittle fracture due to low temperature. On the other hand, although the humidity is high, because the surface temperature of the evaporator is usually below the freezing point, water will condense into frost on its surface. The frost layer, to a certain extent, plays a role in isolating the air, reducing the direct contact between the evaporator and the humid air and thus reducing the risk of corrosion. At the same time, most modern freezers are equipped with a reasonable defrosting system, which defrosts the evaporator regularly. This not only prevents the frost layer from being too thick and affecting the refrigeration effect but also avoids the damage of the evaporator caused by long - term frosting.
In daily use, as long as the freezer is used and maintained correctly, the service life of the evaporator can be further guaranteed. For example, users should avoid frequently opening and closing the freezer door to reduce the entry of hot air, thereby reducing the frequency of frost formation on the surface of the evaporator. Regularly clean the freezer, including the dust and dirt on the surface of the evaporator, to maintain its good heat - exchange performance and avoid overloading the evaporator due to dust accumulation affecting heat transfer. In addition, when professional technicians perform maintenance on the freezer, they will check the operating condition of the evaporator, promptly discover and handle potential problems such as refrigerant leakage, ensuring that the evaporator is always in good working condition.
Whether from the aspects of structural design, material selection, working environment, and daily use and maintenance, the freezer evaporator has high durability. Under normal circumstances, it is not easy to break and can stably provide reliable support for the refrigeration work of the freezer for a long time.
From the perspective of structural design, the structure of the freezer evaporator is relatively simple and stable. There are various common forms of evaporators. For example, the aluminum plate blown - up evaporator often used in direct - cooling freezers is formed by molding two aluminum plates and blowing them up in between. This structure gives the evaporator good integrity, reducing problems such as component loosening and wear caused by a complex structure. For the fin - tube evaporator in air - cooling freezers, by closely combining the fins with the coils, the heat - exchange area is increased. At the same time, the layout and fixing methods of the coils are carefully designed to withstand the pressure changes generated by the refrigerant flowing in the tubes and the thermal stress brought about by the alternation of heat and cold, maintaining structural stability during long - term operation.
The selection of materials plays a crucial role in the durability of the evaporator. Nowadays, most freezer evaporators are made of aluminum or aluminum - alloy materials. Aluminum has the characteristics of being soft in texture and having good heat transfer performance, which can efficiently transfer cold energy to meet the refrigeration needs of the freezer. Moreover, the chemical properties of aluminum are relatively stable, and it has good corrosion - resistance in the general usage environment of the freezer. In contrast, some other metals may be more easily affected by factors such as the humidity inside the freezer and the refrigerant, leading to rust and corrosion, thus shortening the service life. For example, iron - made materials are prone to rust in a humid environment. Once rust occurs, it not only affects the heat - transfer efficiency of the evaporator but may also cause the pipeline to perforate, resulting in refrigerant leakage and ultimately damaging the evaporator. However, aluminum - made evaporators can effectively avoid these problems and greatly improve their own durability.
Analyzing from the working environment, although the temperature inside the freezer is low and the humidity is high, the damage to the evaporator in this environment is relatively limited. On the one hand, when the evaporator is designed, the influence of the low - temperature environment is taken into account, and the selected materials and manufacturing processes can adapt to this low - temperature working condition without problems such as brittle fracture due to low temperature. On the other hand, although the humidity is high, because the surface temperature of the evaporator is usually below the freezing point, water will condense into frost on its surface. The frost layer, to a certain extent, plays a role in isolating the air, reducing the direct contact between the evaporator and the humid air and thus reducing the risk of corrosion. At the same time, most modern freezers are equipped with a reasonable defrosting system, which defrosts the evaporator regularly. This not only prevents the frost layer from being too thick and affecting the refrigeration effect but also avoids the damage of the evaporator caused by long - term frosting.
In daily use, as long as the freezer is used and maintained correctly, the service life of the evaporator can be further guaranteed. For example, users should avoid frequently opening and closing the freezer door to reduce the entry of hot air, thereby reducing the frequency of frost formation on the surface of the evaporator. Regularly clean the freezer, including the dust and dirt on the surface of the evaporator, to maintain its good heat - exchange performance and avoid overloading the evaporator due to dust accumulation affecting heat transfer. In addition, when professional technicians perform maintenance on the freezer, they will check the operating condition of the evaporator, promptly discover and handle potential problems such as refrigerant leakage, ensuring that the evaporator is always in good working condition.
Whether from the aspects of structural design, material selection, working environment, and daily use and maintenance, the freezer evaporator has high durability. Under normal circumstances, it is not easy to break and can stably provide reliable support for the refrigeration work of the freezer for a long time.
This batch of products seems to be of good quality.